In the world of automotive and commercial refrigeration, understanding the nuances between refrigerants is crucial for both efficiency and environmental impact. The terms 134a and R134a might appear interchangeable but there is a distinct difference, as confirmed by technical experts and industry regulations.
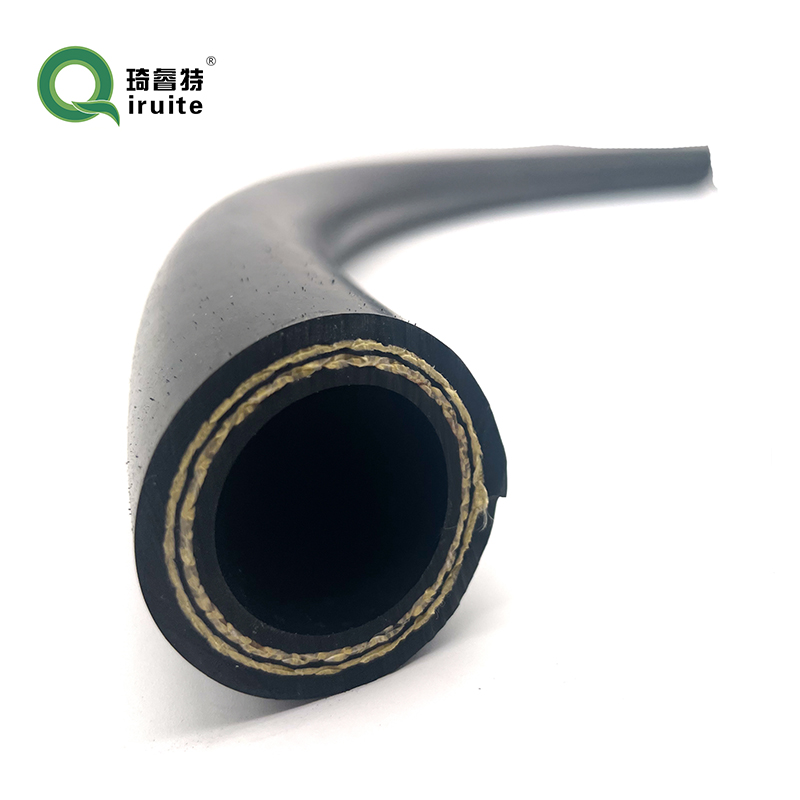
First, both 134a and R134a are references to the same chemical compound known as tetrafluoroethane, a hydrofluorocarbon (HFC) with the molecular formula CH2FCF3. However,
the key difference lies in the context and precision of usage. R134a is the official designation within the ASHRAE refrigerant numbering system. This system is used ubiquitously in HVAC engineering to ensure clarity and accuracy. In contrast, the term 134a tends to be more colloquial and less formal, occasionally used in informal settings or older documentation.
The prominence of R134a arose during the early 1990s as a response to the environmental hazards posed by its predecessor, R12, a chlorofluorocarbon (CFC) that was found to deplete the ozone layer. R134a emerged as an environmentally safer alternative due to its zero ozone depletion potential (ODP), although it is noted for a high Global Warming Potential (GWP) of 1430. This highlights the ongoing balance industries must maintain between performance, environmental impact, and regulatory compliance.
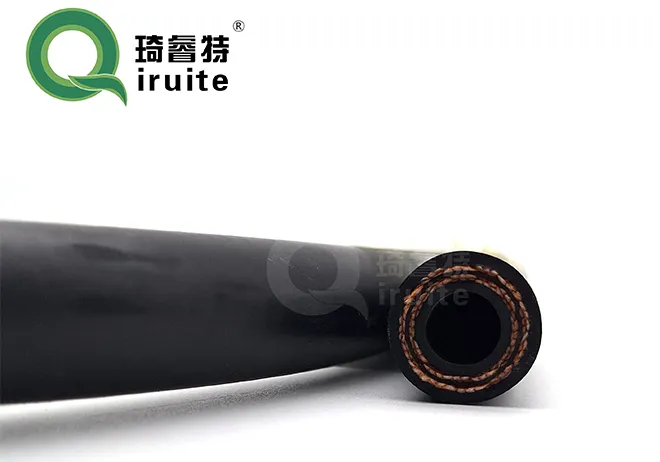
Performance-wise, R134a is applauded for its relatively low toxicity and non-flammability, making it a popular choice for automotive air conditioning systems and commercial refrigeration units. Technicians and engineers value its wide operating range and compatibility with a variety of lubricants, which facilitates its integration into existing systems that previously used R12.
what is the difference between 134a and r134a
From a technical perspective, when dealing with R134a, precise understanding of thermodynamic properties is critical for optimal application. Its efficiency can be enhanced through system designs that incorporate specific coils or compressors tailored for R134a, ensuring better thermal exchange and energy use. Furthermore, regular system maintenance, including leak checks and pressure testing, is indispensable in prolonging the lifespan of systems using R134a and adhering to environmental protection guidelines.
When considering tackling issues such as leaks or performance degradation in systems using R134a, HVAC professionals emphasize the importance of utilizing certified recovery and recycling equipment. This not only helps in maintaining compliance with environmental regulations but also conserves resources by enabling the recycling of refrigerant materials.
From a market standpoint, the demand for R134a remains robust; however, shifts towards more sustainable alternatives such as R1234yf are notable. This transition is driven by stringent climate policies and the introduction of refrigerants with lower GWP. Despite this, infrastructural inertia and the established safety record of R134a suggest it will continue to have a significant albeit diminishing presence.
In conclusion, whether one refers to it as 134a or R134a, understanding the application context, environmental ramifications, and technical specifications is critical. With global efforts converging on climate change mitigation, the future of refrigerants, including R134a, lies in innovation towards less impactful alternatives without compromising on efficiency and safety. This necessitates a rigorous approach to refrigerant selection, informed by both current regulatory guidelines and anticipated environmental trends.