In the realm of automotive engineering and industrial design, the importance of reliable components can never be overstated. When it comes to air brake systems, the air brake hose fitting plays a pivotal role, ensuring the efficient and safe operation of heavy-duty vehicles. Amidst fierce competition and a plethora of choices, understanding the nuances of this essential component can make all the difference for manufacturers, distributors, and end-users alike.
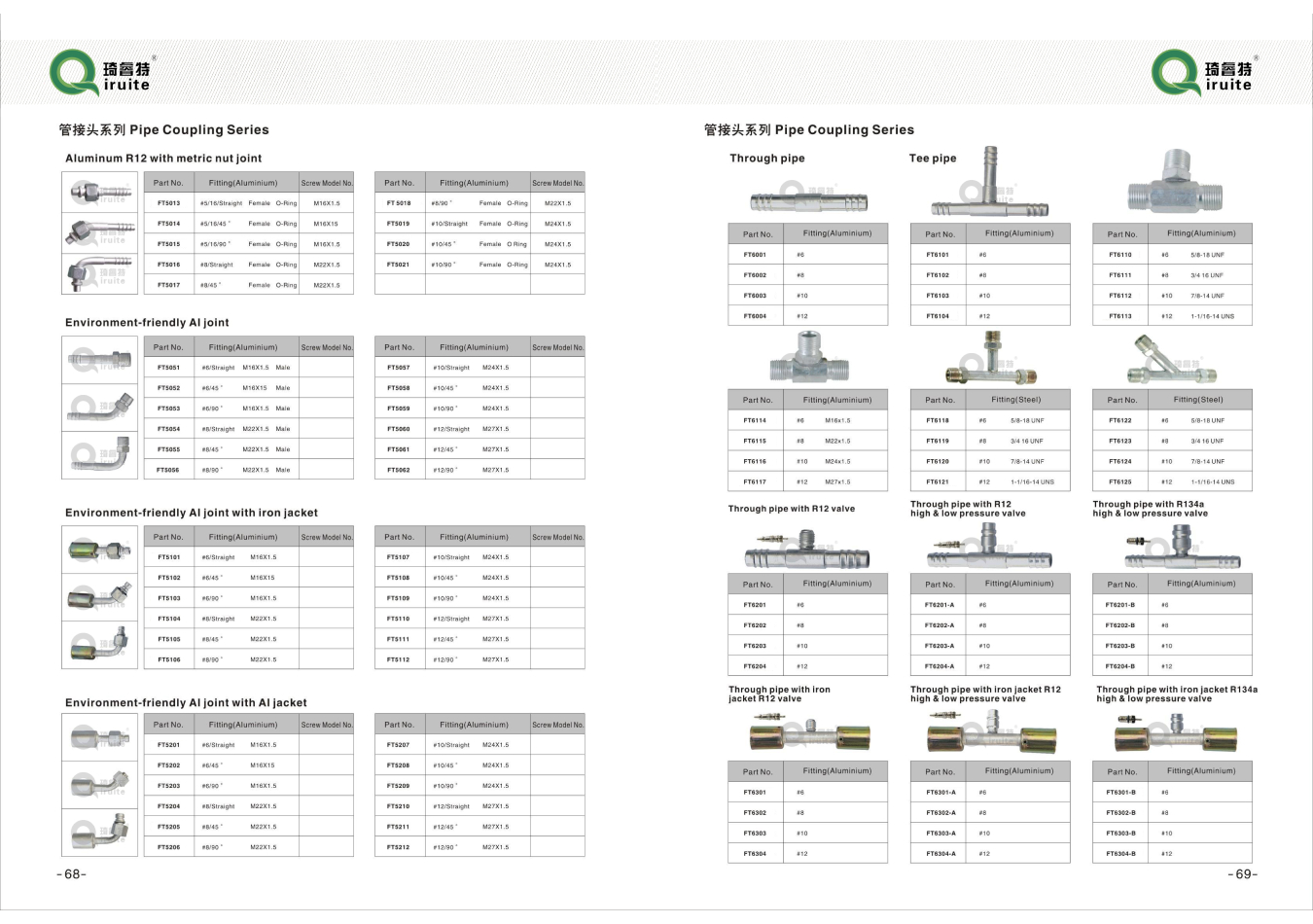
Air brake hose fittings connect brake hoses to the brake line system, providing secure and leak-proof junctions that withstand high pressure. This might seem straightforward, but the precision engineering and material choice behind each fitting are crucial for operational reliability. The fittings must endure harsh environmental conditions, resist corrosion, and maintain performance under fluctuating temperatures and pressures.
Experience dictates that selecting the right material for these fittings can significantly impact their longevity and performance. Brass, stainless steel, and nickel-plated steel are commonly used since they offer excellent resistance to rust and corrosion. The choice largely depends on the specific application requirements and environmental factors the vehicle will face. For colder climates or regions with high humidity, stainless steel fittings are often recommended due to their superior corrosion resistance compared to other materials.
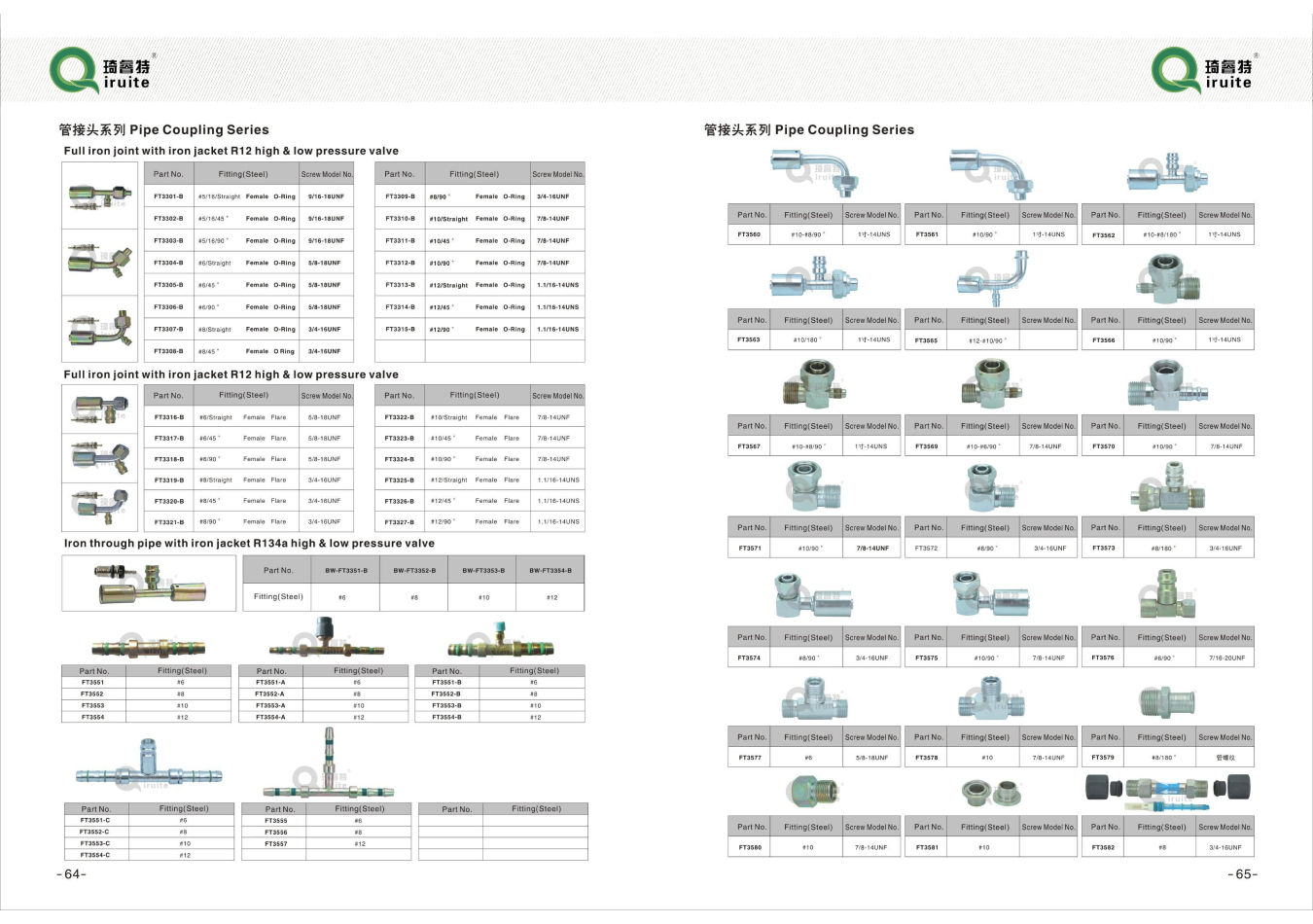
Expertise in the domain of air brake systems further highlights the importance of thread specifications and compatibility with existing hoses. Universal thread standards such as NPT (National Pipe Thread) or BSP (British Standard Pipe) ensure that the fitting integrates seamlessly with various hose types, reducing the risk of leaks and system failures. Additionally, those with experience recognize the value of conducting regular inspections and maintenance.
Air brake hose fittings, like any mechanical component, are subject to wear and should be routinely checked to prevent unexpected failures.
air brake hose fitting
Authoritativeness in the industry is built on understanding not just the components themselves, but the regulatory standards governing them. The Department of Transportation (DOT) in the United States, for example, sets forth rigorous standards for air brake systems on commercial vehicles. Compliance with such standards is non-negotiable for manufacturers aiming to establish credibility and trust in the marketplace. Ensuring that fittings are DOT approved is a testament to their quality and reliability.
Trustworthiness in supplier relationships hinges on transparency about manufacturing processes and quality assurance protocols. Manufacturers that uphold stringent quality control measures and provide comprehensive documentation earn the trust of distributors and end customers. Furthermore, offering training and support in installation and maintenance can cement a manufacturer's reputation as a partner truly invested in the client's success.
In conclusion, air brake hose fittings may be small components, yet they are undeniably critical in the larger scheme of vehicular safety and reliability. Manufacturers and suppliers who demonstrate a deep understanding of the technical, regulatory, and market landscape will be well-positioned to lead in this competitive industry. For end-users, knowledge and due diligence in choosing these fittings are imperative to ensure the safety and efficiency of their brake systems.