Choosing the right hose and couplings for industrial applications is a crucial task that demands more than just a basic understanding of specifications. Each piece of equipment carries a distinct set of requirements, and adhering to these precise needs not only ensures optimal performance but also underlines safety and durability.
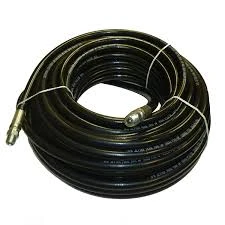
Industrial hoses come in various materials, each serving a specific purpose. For instance, rubber hoses are popular due to their flexibility and resilience, making them ideal for transporting gases, liquids, and abrasive materials. Meanwhile, thermoplastic hoses are preferred in scenarios where a lightweight and versatile solution is necessary. They're particularly effective in high-pressure systems due to their endurance and ability to sustain a wide temperature range.
The coupling, often overlooked, plays an equally critical role in the system's functionality. Quick-release couplings, for example, are invaluable in operations requiring frequent connection and disconnection. They provide a secure fit that prevents leaks, which is essential in maintaining system efficiency and safety. Threaded couplings, although perhaps more time-consuming to connect, offer a dependable seal ideal for long-term setups.
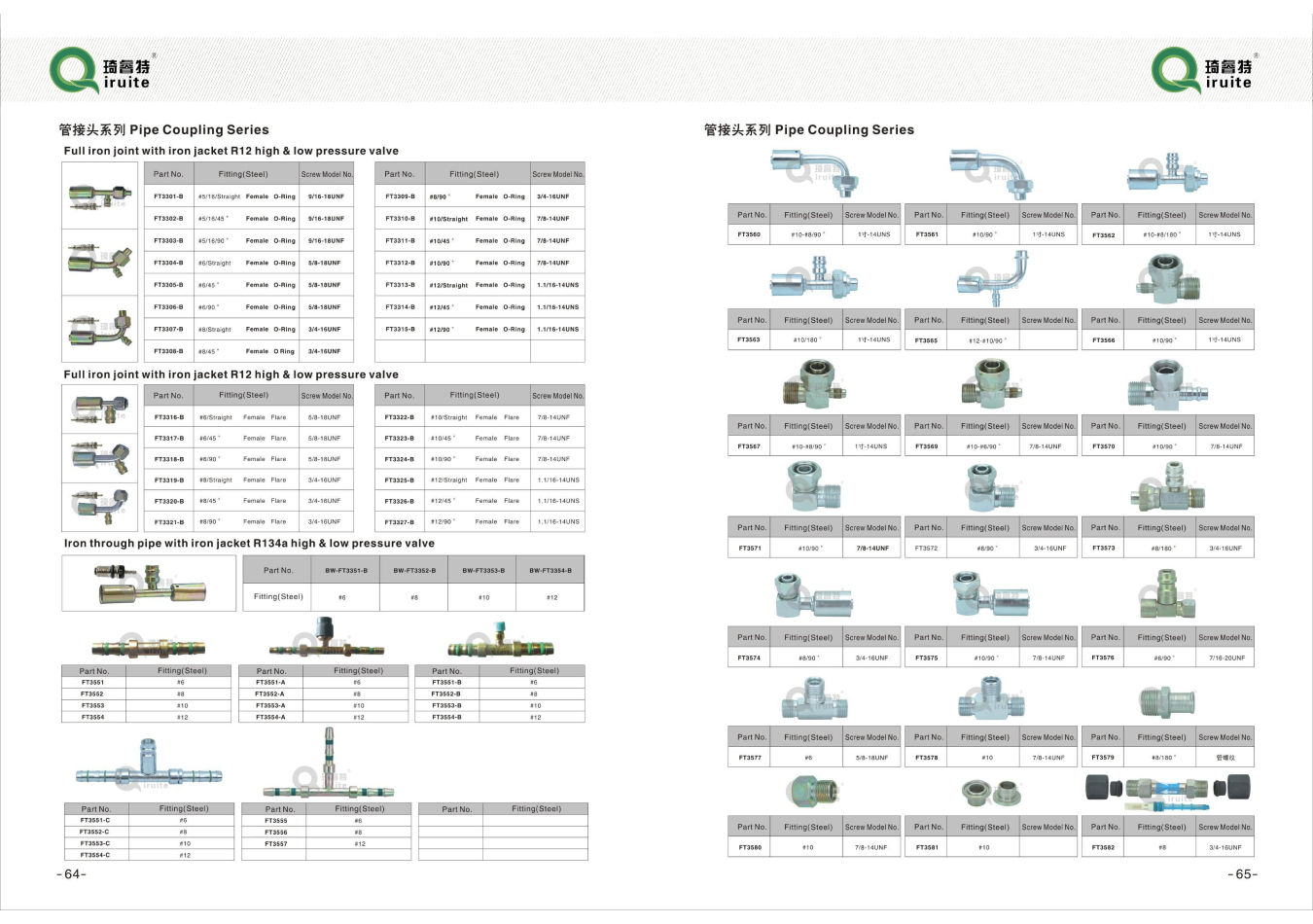
For someone selecting hose and couplings, real-world experience matters immensely. Consider the story of a high-volume factory manager who switched to polyurethane hoses paired with cam-lock couplings. This adjustment was prompted by frequent maintenance issues with previous PVC hoses and threaded couplings, which led to numerous unanticipated downtimes. The switch resulted in a significant performance boost due to the superior wear resistance of polyurethane material and the reduced connection time offered by cam-lock couplings. This simple change not only enhanced productivity but also minimized long-term costs associated with repairs and replacements.
From an expertise standpoint, understanding the manufacturer’s specifications and industry standards is paramount. For hoses, parameters like diameter size, maximum operating pressure, and temperature tolerance should closely align with your machinery’s demands. The coupling should match these specifications to avoid system failures. DIN and ANSI are two standards often referred to, providing guidelines on dimensions and pressure ratings to ensure compatibility and safety.
hose and couplings
Authoritativeness in the topic of hose and couplings often comes from being well-versed with compliance regulations. Industries with stringent standards, such as the food and pharmaceutical sectors, require hoses that are FDA-approved and have smooth interiors to prevent bacterial growth. Couplings, similarly, must conform to strict hygiene standards, often necessitating the use of stainless steel for its non-corrosive properties.
Building trustworthiness around hose and coupling products involves transparent communication and availability of third-party verifications. TÜV and NSF certifications offer additional assurances of quality and safety, providing users confidence in the product’s performance. Companies committed to adhering to these certifications typically maintain documentation and testing results that are readily accessible for consumer review.
In many industrial operations, customizable solutions tailored to specific applications are vital. This bespoke approach might involve custom lengths, particular materials that meet unique chemical resistance needs, or varying flexibility levels. Engaging with manufacturers capable of offering personalized solutions increases the likelihood of achieving an optimal fit, enhancing overall system efficiency and longevity.
Finally,
ensuring the longevity and performance of hoses and couplings necessitates a rigorous maintenance plan. Regular inspections for wear, punctures, or leaks can prevent catastrophic failures. Training staff to handle hoses properly and to understand the significance of maintenance can avert unnecessary damage. Keeping a log of inspections and repairs provides a historical record that helps predict future needs and budget accurately for maintenance expenses.
To sum up, choosing the correct hose and couplings involves an intricate balance of experience, technical knowledge, regulatory awareness, and committed maintenance. By approaching this task with a comprehensive mindset grounded in authoritative sources and real-world experiences, one can ensure a durable, effective, and safe industrial system.